
#Free cad program to analyze truss full
I drew the joint full scale, and had a plastic overlay with the punched hole layout on it then I could start to size the plates I needed, by shifting this plastic sheet around for a best fit. Then, for the most part, it is just how many nails do I need, parallel to the grain, for that member’s load keeping end and edge dist. We know what the shear value for a 16d x 1.5" or 1.25" nail in that plate is in a tight hole, and can make some generalizations about buckling loads, etc. Now, tooth orientation is out of the picture. Maybe the simplest repair solution for you and me is just a perforated plate, in several different gages, and many sizes. years ago, when the world was a simpler place, and would have to do some serious review to come up to speed with the current codes and methods. The plate people also have tons of testing on which to base adjustment factors, etc. I would guess that most of this would be revealed by a close look at the TPI literature and at the plate manufacturers literature and their ICC ES reports. plate gage will come into play, and the teeth have one allowable load, as a function of the wood density, when the load is perpendicular to the tooth face and another when the load is in the plane of the tooth and Hankinson’s formula might even be applied to the wooden members to determine the controlling tooth value. Then, to the actual joint design, they probably have an algorithm which goes something like this: given the size and geometry of the members coming into a joint and the loads on the members from the truss analysis they mask out edge and end distances on each of the members which are not allowed to count, even though they may be partially effective compression members will act in end bearing on adjacent members to transmit part of their loads now how big a plate, from our stock, do I need to pick up the loads from each member? Plate buckling vs. As has been suggested, any good program will analyze the truss members, but maybe not as efficiently as their proprietary program does, and theirs spits out cutting dimensions and angles to boot. Otherwise, I suspect they keep the actual coding (internal operations and methods) pretty well locked up in their little black boxes. If you could show them enough business, I suspect they might be more cooperative. They’ll let you (your truss design dept.) use them if you are going to manufacture trusses and use truck loads of their plates each year. Those types of programs are proprietary to the plate manufacturers like MiTek, and their own testing of their products.
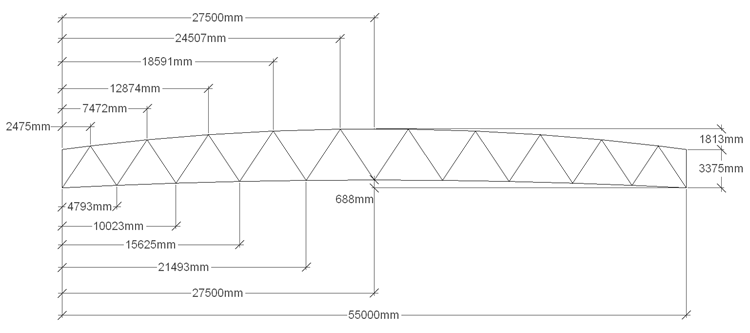
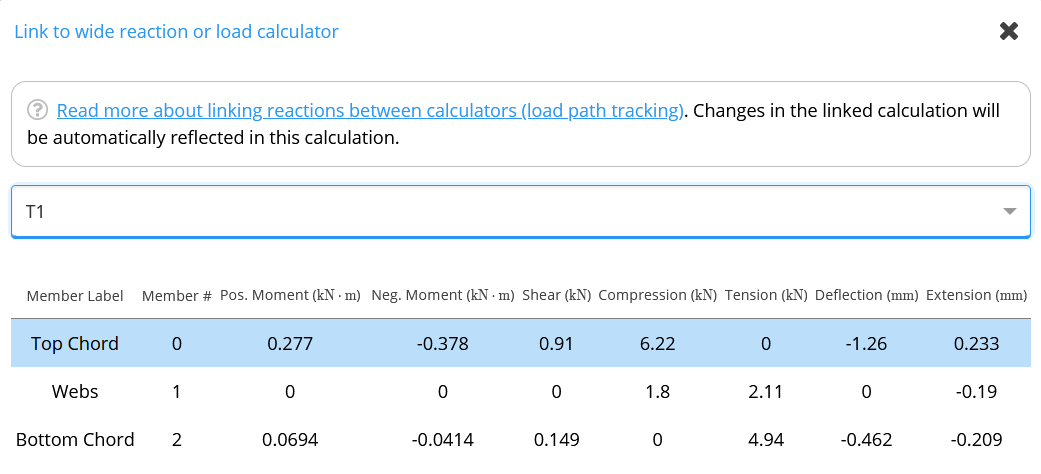
#Free cad program to analyze truss software
RE: Alternative to Mitek Wood Truss Software msquared48 (Structural) 30 Aug 13 16:35 That's where I would assume the proprietary wood truss companies (MiTek) has a lot of internal rules for setting this connection rigidity. The only tough part is knowing how rigid or non-rigid you want to make the connection. Honestly, it's not really all that difficult.
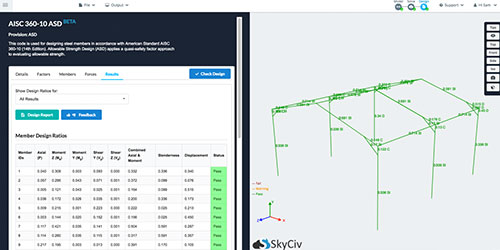
Reduce the properties and you will get closer and closer to an idealized pinned connection. If the link beam has properties identical to the member which it is replacing then it will behave as a fully fixed connection.
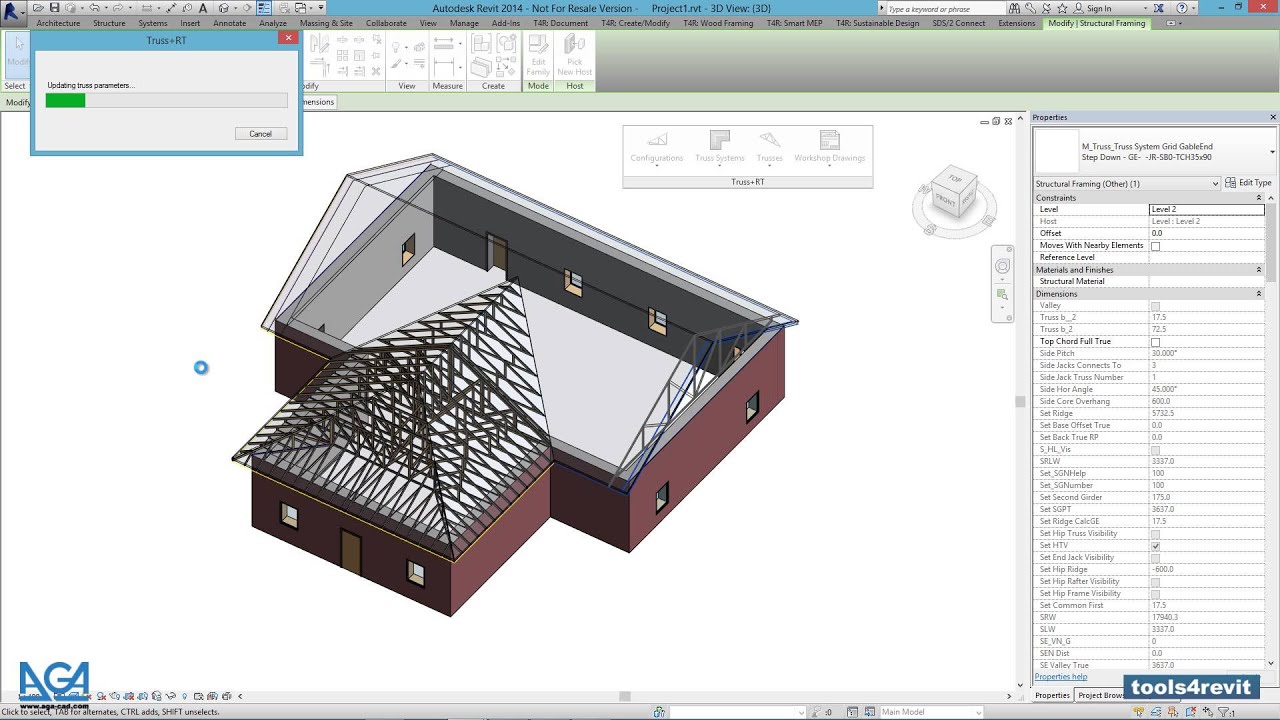
You can then adjust the rigidity of the connection in any direction by changing the properties of this link beam. This link beams would have fully fixed end releases on both ends. What I usually tell people (when they want to do this type of thing in RISA) is to model a small link beam for the connection. There are ways to do this in RISA, but it is not very common. My guess is that you need the plate connections to be modeled as having some connection rigidity rather than as idealized pinned or as idealized fixed connections.
